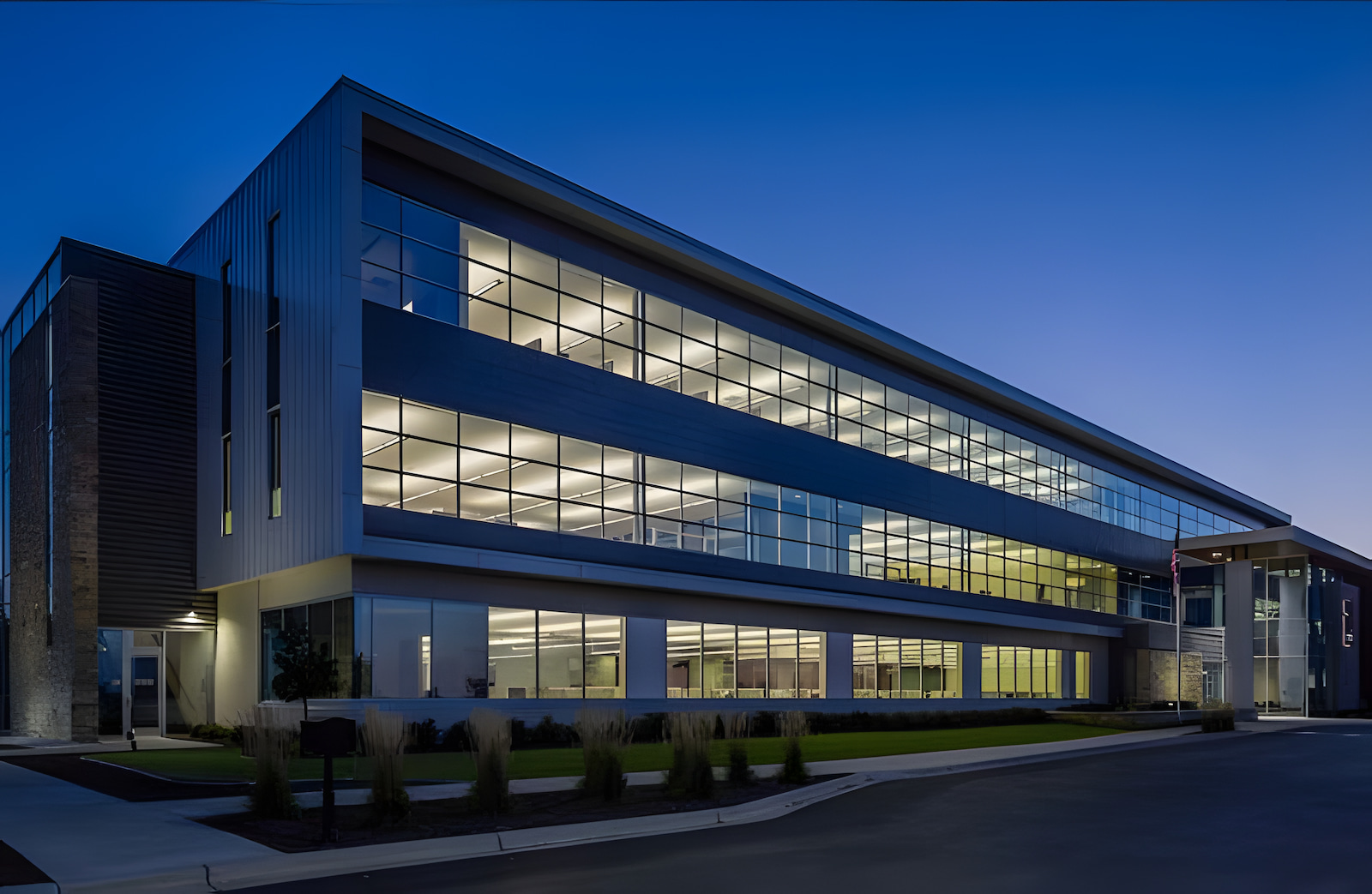
In This Article
Impossibly tight deadlines and problem-solving on the job site are two of the challenges Hurckman crews face regularly. Learn how one commercial customer faced those challenges head-on.
Rapid growth led Navitus to expand its Appleton facility only three years after it opened. A new 120,000-square-foot, four-story Appleton building is 70 percent larger than the original construction and was constructed in a compressed timeline. On this job, Hurckman provided service for all mechanical installation, commercial HVAC services, and commercial plumbing services on a job that only allowed six months of work on site.
Hurckman crews made the decision to pre-fabricate all ductwork and piping at the Hurckman shop. Doing so allowed crews to work faster, maintain quality, and make deadlines. All piping was pre-assembled in the shop with appropriate valves and outlets. Sheet metal was pre-insulated in the shop so crews could quickly make needed connections on the job site.
This was one of the first jobs where Hurckman crews tracked daily output. Every day, crews logged how much pipe and ductwork was installed which allowed the team to track daily metrics. According to HVAC foreman Mark LeMere they were able to better monitor job flow and more accurately plan work schedules and material ordering. This system contributed to the team’s ability to meet the job’s timeline.
Hurckman crews were tasked with finding innovative design/build solutions while on site.
- Due to the tight timeline, teams decided to cast trapeze hangars in place before the cement floors were poured. This allowed piping, plumbing, ventilation, and electrical systems to share hangars and save time in installation.
- The three boilers in the basement of the building needed to be vented through the roof four stories above. “We basically reached the limits on venting,” LeMere said, so he re-designed the boiler room moving the boilers to a north-facing wall to cut down on the distance for venting.
- Hurckman crews installed miles of piping much of which was re-designed on site. Original piping specifications did not fit into the ceiling heights and the design called for exposed ductwork. Crews had to custom fabricate ductwork that was wider and shorter than original specs, yet fit in between structural steel beams and the ceiling.
- The entire building is faced with glass, but the intense sun on the south side of the building triggered the air conditioning in winter. After construction was finished, Hurckman crews went back on-site to re-direct air flow and make the environment more comfortable for occupants.
Air handling units were installed on each floor, but on one floor the unit was directly above a conference room and made too much noise. Hurckman crews designed a new route for the duct and lined it with sound-absorbing insulation on the inside. They also put noise cancellation material on the outside of the duct to further decrease noise. Additionally, they put a control on the fans so they would ramp up more slowly and limit the highest speed.
The result: the project was completed on time thanks to hard work from crews on site and in the shop. To learn more about how Hurckman’s services can help your next project, please contact us.