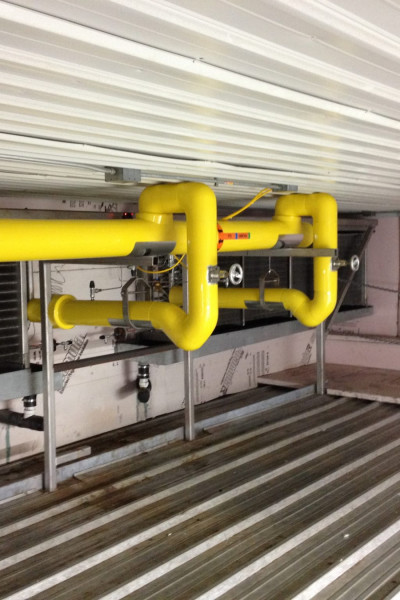
Condenser Replacement
Increased production drives upgrade in cooling; new equipment saves thousands in energy costs annually.
The Challenge
After a large expansion in their yogurt production line, Klondike Cheese noticed the discharge pressure on their cooling line was dangerously high to meet expanded cooling needs. The company was running the risk that extra loads on the old compressors would release ammonia into the atmosphere.
The Solution
Hurckman selected updated equipment and designed a platform to solve the problems with increased production. Crews recommended an ATC-E Evaporative Condenser because of its high capacity and quiet operation. Working collaboratively with Carter Machine, crews designed, fabricated and installed a platform for the new unit that featured a platform with safety railings around the condenser allowing safe access for routine maintenance. The retrofit also included a higher capacity stainless steel water sump with a self-cleaning, conical bottom. The taller tank allowed higher suction to the pumps, equating to lower horsepower needed, thus saving money. Crews lifted the new 50,000-pound condenser on top of the building.
The Results
Hurckman also provided a customized plant energy savings study. As a result of smaller condenser fans, reduced energy usage and reduced head pressure in the compressor, the company will conservatively save between $50,000-$60,000 annually in energy costs.
Explore Similar Projects
-
-
Expand Malt Drying System
-
New Chiller Room
Promise Delivery
We don't just meet expectations, we exceed them. Your project's success is our commitment.